Coreroom
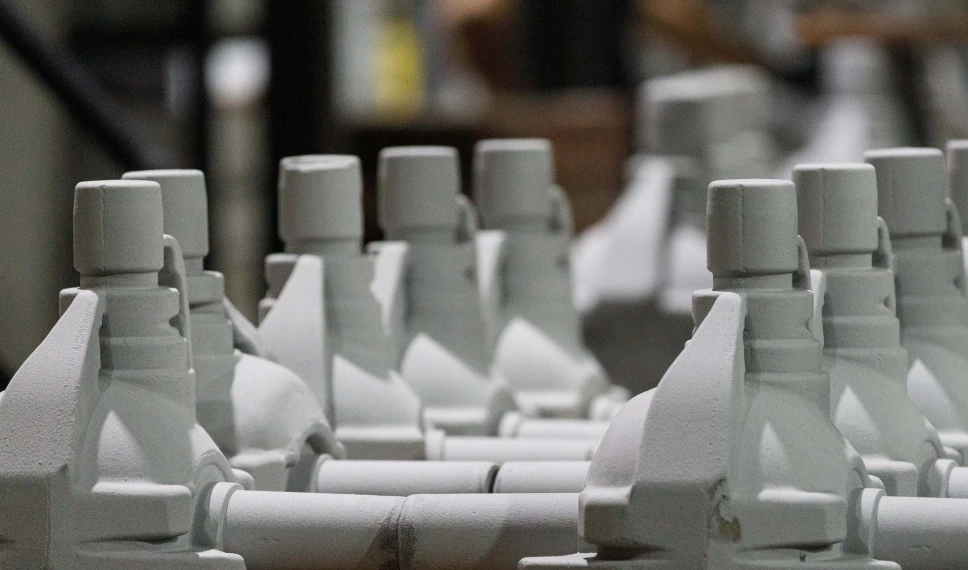
A coreroom is a plant where cores are produced and applied, which are used in the process of casting iron and make the casting perfect. Core models are compacted sand masses of choice to form small figure gaps that need to be processed into casting but cannot be formed through the mold. Cores, which are high-temperature resistant bodies, are of great importance in the iron casting industry because they directly affect the quality of parts.
The core, which is used to shape melted and liquid iron, helps the casting parts to be expertly given any desired shape. The core, which contributes to the successful execution of the casting process, is obtained by mixing silica sands and organic binders and hardening them by cooking or chemical reaction.
The most effective method of producing cores is the Cold-Box system. In the Cold-Box system, the sand that will form the core is mixed with two separate binders and hardens spontaneously without any cooking process thanks to the gas catalyst. In this way, time and energy are saved in the production of cores. The Cold-Box method is performed by recording the required pressure and gas times to the product ID in the quality management system and applying the necessary production processes. After the process, high quality cores are obtained and sent to the foundry.
Core Machines
- “1 piece DISA 40 L” Core Machine
- “1 piece Hottinger 25 L” Vertical Core Machine
- “1 piece Hottinger 20 L” Vertical Core Machine
- “3 piece Hottinger 12 L Horizontal Core Machine
In Kutes Metal coreroom, cores are painted with alcohol or water-based paint before they are placed in the mold, and Lazyou double-band core drying oven is used in the drying process of cores painted with water-based paint. In this way, all the cores produced in the cores are of equal quality.